what is agv battery?
Let’s first understand what AGV is. AGV stands for Automated Guided Vehicle, which is a transport vehicle equipped with electromagnetic, optical, or other automatic guidance devices. It can travel along a specified guidance path, providing safety protection and various material handling functions. With the widespread application of 5G technology and artificial intelligence in the field of industrial robotics, AGV mobile robots are widely used in flexible production lines. They are the optimal choice for many manufacturing enterprises to improve production efficiency and reduce production costs, showing explosive growth in recent years. AGV carts have advantages such as fast movement, high efficiency, simple structure, strong controllability, and good safety.
AGV batteries are specifically designed for use in automated guided vehicles. These batteries provide the energy needed to drive the AGV. AGVs can autonomously move in scenarios like production lines, warehouses, and logistics centers. If the battery level is low, the AGV won’t be able to function properly.
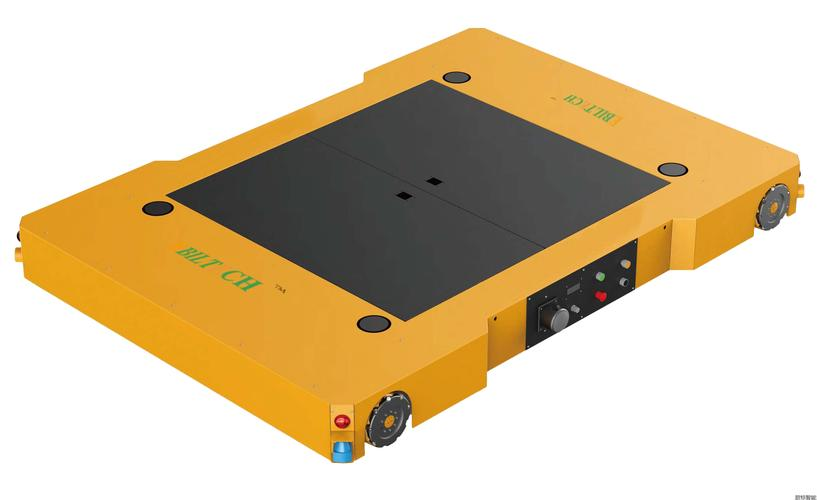
Advantages of AGV (Automated Guided Vehicle)
Cost-Effective: AGVs offer a low cost with a high return on investment in the current industrial mobile robotics field. The cost-effectiveness is a key factor in the decision-making process for customers, and AGVs are often a more economical solution.
High Efficiency: AGV carts can achieve automatic charging, enabling 24-hour continuous operation and significantly improving the efficiency of product and material handling.
Saving Management Efforts: AGVs implement digital management, providing insights into material transport progress through data panels, thereby enhancing management efficiency.
High Reliability: Compared to manual handling with its inherent inefficiencies and uncertainties in forklift and trailer paths, speeds, and safety, AGVs offer controlled travel paths and speeds, precise positioning, and centralized management systems. This greatly improves the efficiency of material handling, and the central management system allows for comprehensive monitoring, significantly enhancing reliability.
High Safety Standards: AGVs come with advanced safety features, including intelligent traffic route management, collision avoidance, warnings, emergency braking, and fault reporting.
Wide Range of Applications: AGVs play a crucial role in various manufacturing processes such as warehousing and assembly. They have become one of the most symbolic configurations in modern smart factories.
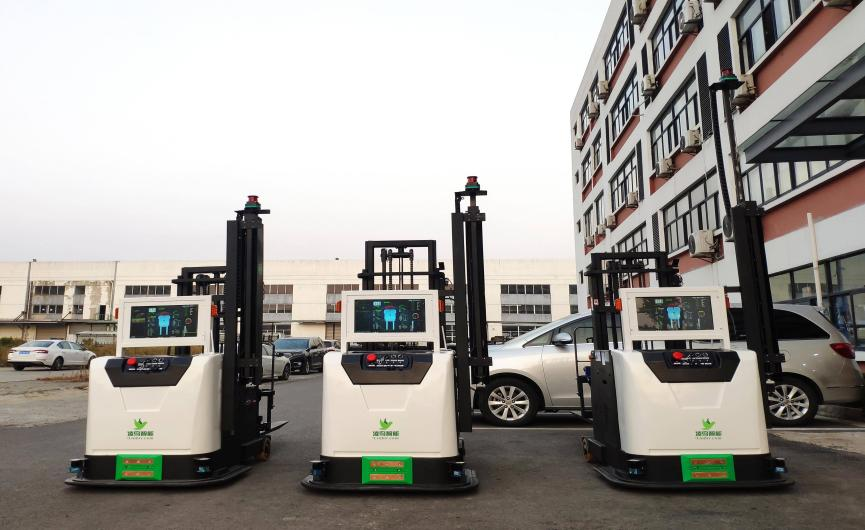
Characteristics of AGV Batteries
Characteristics of AGV Batteries:
AGV batteries possess features of safety, reliability, environmental friendliness, and energy efficiency, meeting various high-performance requirements.
Safety: AGV batteries employ safe and efficient battery technologies during usage to avoid overcharging, overcurrent, and overdischarging.
Reliability: AGV batteries can operate reliably in high-temperature, low-temperature, and highly corrosive environments, enhancing overall reliability.
Environmental Friendliness: During usage, AGV batteries do not contain any toxic components, preventing environmental pollution.
Energy Efficiency: AGV batteries are designed to support efficient operation while maintaining low energy consumption.
Types of Batteries for AGV Robots
Currently, most AGV robots on the market use nickel-cadmium batteries, nickel-metal hydride batteries, lithium batteries, and lead-acid batteries.
1.Nickel-Cadmium Batteries: The positive electrode is nickel hydroxide, the negative electrode is cadmium, and the electrolyte is a potassium hydroxide solution. Nickel-cadmium batteries can undergo more than 500 charge-discharge cycles, making them economically durable. They have low internal resistance, allowing for fast charging, providing large currents to the load during discharge, and exhibiting minimal voltage changes during discharge. The most significant drawback of nickel-cadmium batteries is the occurrence of a severe “memory effect” if not handled properly during charge and discharge, significantly shortening their service life.
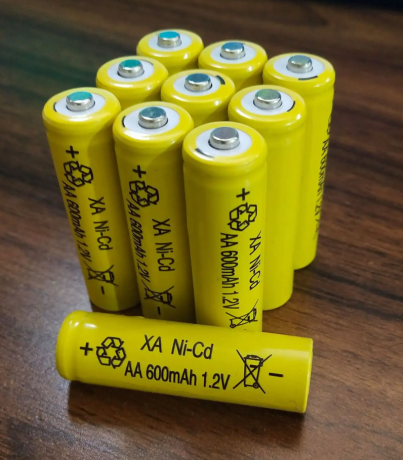
2.Nickel-Metal Hydride Batteries: They use a large amount of metal materials with good conductivity, can handle high-power discharge, have a high cycle life, are pollution-free, and are resistant to overcharging and over-discharging. The energy density of nickel-metal hydride batteries is twice that of nickel-cadmium batteries. They exhibit better self-discharge performance than nickel-cadmium batteries, can retain a charge for a longer time after charging, and have high recycling value. However, the downside includes high raw material costs and low charging efficiency. Even in an idle state, the charging efficiency of nickel-metal hydride batteries is less than 100%. After charging exceeds 80%, secondary reaction rates increase rapidly, leading to a quick rise in heat generation and potentially causing thermal runaway.
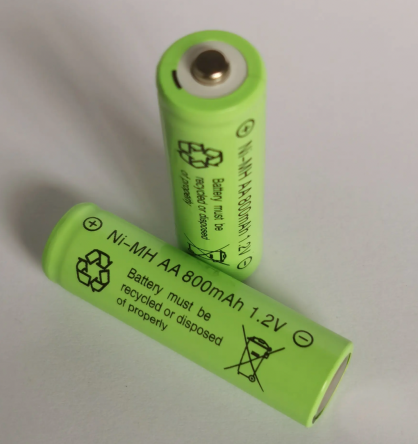
3。Lithium Batteries: These batteries use lithium metal or lithium alloy as positive and negative electrode materials and a non-aqueous electrolyte solution. They have high energy density, maintain high voltage (average voltage of 3.6V), which is three times that of nickel-cadmium and nickel-metal hydride batteries. Lithium batteries have a flat and high capacity voltage, a wide operating temperature range (-20°C to 60°C), long charge-discharge cycles, and a capacity retention rate of at least 70% after 500 cycles. They are widely used due to their safety, low memory effect, small size, light weight, and are commonly found in everyday devices such as mobile phones.

4.Lead-Acid Batteries: Lead-acid batteries exhibit good reversibility, stable voltage characteristics, wide applicability, abundant raw materials, and low production costs. However, they have clear disadvantages, including safety hazards with potential explosions during intense collisions, posing a threat to human life. Lead, a significant component, can lead to environmental pollution if not properly handled after disposal. Lead-acid batteries also exhibit a memory effect, with frequent operation in a state of incomplete discharge leading to a rapid reduction in capacity below the rated value.
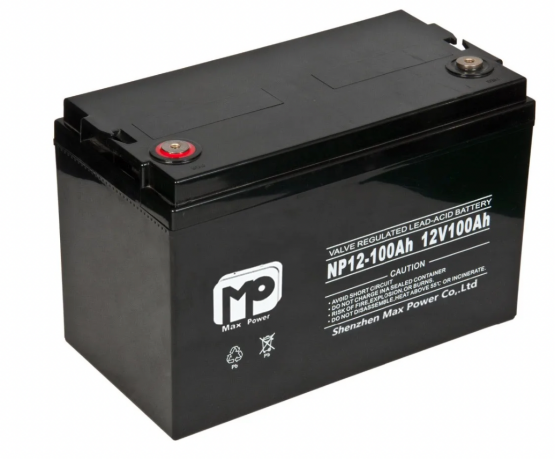
·How to choose AGV lithium batteries?
Communication Protocol: Currently, AGV lithium batteries support communication protocols such as RS485, RS232, and CAN. The selection of the battery’s Battery Management System (BMS) control module should be based on the communication protocol.
Voltage: Consider the rated output voltage and maximum voltage at the output end, and be clear about the lithium battery’s voltage and raw materials. The rated voltage of the battery should not be less than the rated voltage of the electric motor. The fully charged voltage of the battery should not exceed the maximum voltage of the machine equipment.
Power Consumption: For applications with high power consumption or discharge, where the lithium battery capacity exceeds 1.5 kWh, it is recommended to use iron phosphate lithium batteries, taking into account the safety factor.
Charge and Discharge Output Power, Battery Charging Output Power: For charge and discharge currents exceeding 60A, it is recommended to use iron phosphate lithium batteries. Under normal conditions, batteries can be charged at 0.5C, which is a common practice. However, in specific applications, many AGV working conditions require rapid charge and discharge due to short charging times during certain battery charging processes. Therefore, a high current of 2C is recommended for fast charging to meet the requirements of rapid charge and discharge cycles in the application.
Application Environment: In extreme natural environments such as high temperatures or challenging road conditions, you may choose to use lithium iron phosphate batteries. For extremely low-temperature conditions, ternary lithium batteries can be considered.
Manufacturer: Considering factors such as the project cost, after-sales service cost, and the possibility of accidents during transportation, it is essential to choose a professional AGV lithium battery manufacturer for customization. In particular, pay attention to the quality of the battery cells, BMS modules, and assembly processes for AGV batteries.
How to Choose AGV Battery Capacity
The rated voltage of AGV charging batteries typically falls between 24V and 48V, varying depending on the AGV model. Choosing the appropriate AGV battery capacity is crucial. If the battery capacity is too small, the AGV will require frequent charging, impacting application efficiency and reliability. On the other hand, if the battery capacity is too large, it may increase production costs, and the weight of the battery could exceed the AGV’s tolerance.
The capacity of AGV charging batteries directly determines the AGV’s working time and load capacity. In general, the capacity of AGV charging batteries should meet the working requirements of the AGV, ensuring it can operate continuously throughout a day or a work cycle. Common capacities for AGV charging batteries include 120Ah, 200Ah, and so on. The choice of battery capacity depends on specific requirements, and the calculation should consider the AGV’s usage time and power demands
Common Charging Methods for AGV
Based on Charging Time:
- Opportunistic Charging and Full Cycle Charging:
- Opportunistic charging allows AGVs to charge without restrictions at docking stations at any time. This helps replenish the energy consumed during work, extending battery life and reducing the required battery capacity. Full cycle charging requires AGVs to completely exit service and enter a designated charging area, charging only when the battery charge drops to a specified range. Some AGVs use a combination of both charging methods.
- Opportunistic Charging and Full Cycle Charging:
Based on Charging Area:
- Onboard Charging and Offboard Charging:
- Onboard charging means AGVs stay on the working route, utilizing brief stops during the work process for charging without dedicated charging times. This method does not occupy work time and is essentially an extension of opportunistic charging. In contrast, offboard charging involves AGVs entering a charging area or specific charging station after completing work.
- Onboard Charging and Offboard Charging:
Based on Operation Methods:
- Manual, Battery Swapping, and Automatic Charging:
- In manual charging, when AGV battery levels are low, the ground control center directs them to designated charging areas or stations for manual charging. This method is secure, reliable, and has lower equipment costs. It is suitable for scenarios with high response speed requirements, fewer vehicles, and more personnel under standard working conditions. During battery swapping, when AGV battery levels are low, human operators replace the battery pack, allowing the AGV to resume operation. This method is costly and has operational complexities, suitable for scenarios with high response speed requirements and insufficient vehicles. Automatic charging involves AGVs automatically reporting and requesting charging when additional power is needed. The ground control center directs them to designated charging areas or stations for automatic charging. After completing the charging, AGVs automatically detach from the charging system and resume normal operation. Automatic charging is suitable for scenarios with long working cycles, more vehicles, and fewer personnel, requiring high automation.
- Manual, Battery Swapping, and Automatic Charging:
Based on Charger Electrical Connection:
- Contact and Wireless Charging:
- Contact charging requires using cables and charging connectors to connect the vehicle to the power supply system for fast charging. However, this method is not suitable for frequent opportunistic charging, as charging connectors can wear out and need regular replacement, posing safety risks. Wireless charging is a non-contact charging method that does not require cables to connect the vehicle to the power supply system. It eliminates the need for charging connectors and allows both the charger and the device being charged to have no exposed conductive points. This technology overcomes the drawbacks of plug-in charging methods, achieves electrical isolation between the charging end and the AGV energy storage system, enhancing safety and widening its applicability. Presently, wireless charging products for AGVs are comparable to contact charging systems, offering features like on-the-go charging and immediate stops, enhancing the automation level of AGV usage. However, wireless charging technology is complex, expensive, and not suitable for AGVs with chargers above 10KW due to their larger size.
- Contact and Wireless Charging:
When is it necessary to replace AGV batteries?
Operational Efficiency:
- When the operating time of AGV gradually shortens each day, it indicates the need for battery replacement.
Power Conditions:
- If AGV vehicles exhibit insufficient power when starting up, indicating a struggle due to the significant power requirements of the engine, it may be a sign that the battery needs replacement.
Maintenance Situations:
- Some AGV vehicles are equipped with displays or dashboards. When the lithium battery malfunctions and the indicator lights up, and repairs cannot resolve the issue, it signals the need for battery replacement.
2 Responses
Hello, We need to find a battery similar than this model, APX12-250 (12V250Ah), Apex brand,
Please contact me for any comment
Regards
Hi Arturo, thanks for your comment. We can produce the similar battery. We sent you one email yesterday. Please check. Thanks.